ESI PAM-COMPOSITES pomaga Kotobukiya Fronte w produkcji wysokiej jakości dźwiękochłonnych dywaników samochodowych
Wyzwanie
W ostatnim dziesięcioleciu do produkcji dywaników podłogowych coraz częściej zamiast gumy stosowane są materiały syntetyczne. Znacznie zwiększyło to trudności produkcyjne. Firma Kotobukiya Fronte, produkująca około 30 różnych złożonych syntetycznych dywaników, musiała szybko zaadaptować nowe projekty i zapewnić wysoką wydajność produkcji.
Korzyści
ESI PAM-COMPOSITES pozwoliło Kotobukiya Fronte szybko i płynnie dostosować się do innowacji w momencie przejścia z dywaników izolujących dźwięk na dywaniki dźwiękochłonne. Oprogramowanie symulacyjne umożliwiło szybie i tanie opracowanie nowych, stabilnych procesów produkcyjnych.
Historia
Około roku 2010 zmieniła się główna funkcja dywanów samochodowych. Nastąpiło przejście z izolacji do pochłaniania dźwięku. Ta ewolucja stała się możliwa dzięki zastosowaniu materiałów syntetycznych zamiast gumy. Ze względu na pozytywny wpływ na środowisko włókien syntetycznych (są lżejsze co przekłada się na mniejsze zużycie paliwa) i ich podwójną funkcje (zarówno absorpcja dźwięku jak i izolacja), stały się one standardem w samochodach. Ich jedynym minusem jest to że wymagają nowych, skomplikowanych procesów produkcyjnych.
Dziś, syntetyczne wykładziny podłogowe stanowią 70% produkcji Kotobukiya Fronte. Aby osiągnąć stabilny proces formowania materiałów syntetycznych, firma musiała pokonać kilka przeszkód niespotykanych dotąd podczas pracy z gumą. Po pierwsze, początkowa grubość syntetycznych materiałów włóknistych wynosi od 10 do 20 mm – dla gumy było to 2,3 mm. Im grubszy jest materiał wsadowy tym trudniejszy jest cały proces.
Drugim problemem są różne wartości grubości na przekroju detalu. Celem procesu jest mocne ściśnięcie materiału w miejscach gdzie wymagana jest wytrzymałość, natomiast niewielkie tam gdzie potrzebna jest absorpcja dźwięku. Aby znaleźć idealny proces częstą praktyką jest przeprowadzanie wielu fizycznych iteracji optymalizacyjnych. Wielowarstwowa struktura dywaników z włókien syntetycznych (trzy warstwy zamiast dwóch w porównaniu do dywanika gumowego) również zwiększa trudność kształtowania.
ESI PAM-COMPOSITES pozwolił zaoszczędzić czas i pieniądze. Narzędzie symulacyjne z powodzeniem przezwyciężyło problemy formowania dając możliwość wirtualnej optymalizacji oraz oceny zachowania różnych materiałów. Pomogło to również inżynierom procesowym określić właściwą kinematykę narzędzi.
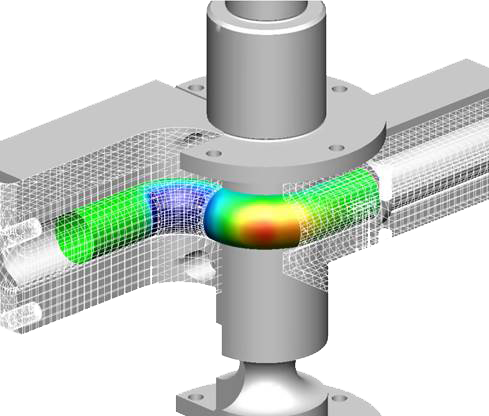